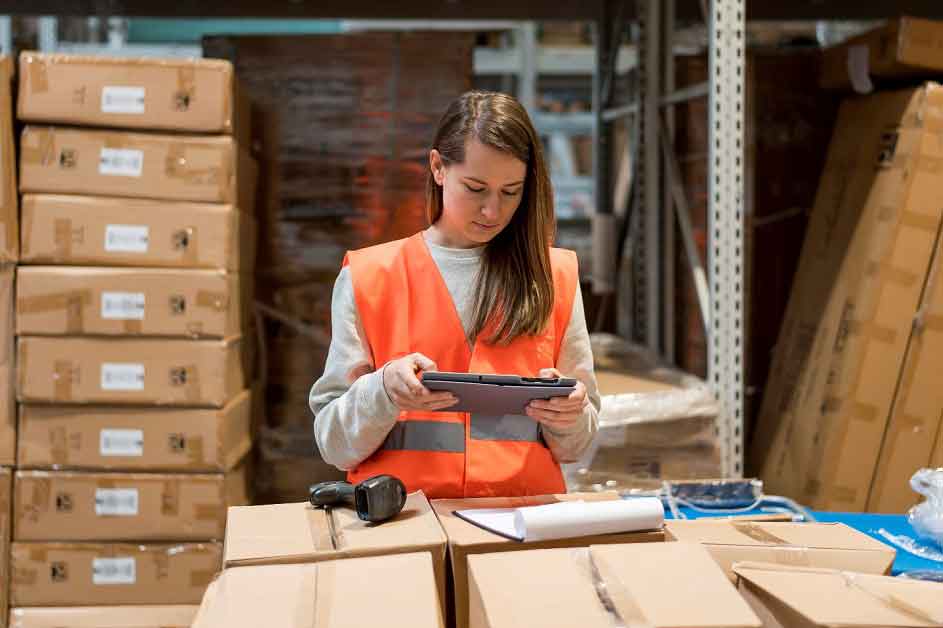
Stock control is an essential aspect of any business that involves the storage and distribution of products. Without an efficient stock control system in place, businesses can face a wide range of issues, from overstocking and stockouts to inaccurate inventory management and lost revenue. In this article, we will discuss the importance of stock control systems, the different types of stock control systems, their components, and the best practices for implementing and optimizing them.
Introduction
Stock control systems refer to the processes and tools businesses use to manage inventory levels, orders, and shipments to ensure they have the right products in the right quantities in stock.
Importance of stock control systems
Stock control systems are crucial to maintaining a healthy balance between supply and demand, minimizing costs, and maximizing profits. They help businesses avoid overstocking, which can lead to increased storage costs, reduced cash flow, and wastage. Similarly, stockouts can result in lost sales, customer dissatisfaction, and damage to the business’s reputation.
Stock control systems offer several benefits, including improved inventory accuracy, better demand forecasting, reduced stockouts and overstocking, lower storage and handling costs, increased operational efficiency, and enhanced customer satisfaction.
Types of Stock Control Systems
– Manual
Manual stock control systems involve tracking inventory levels and orders manually using spreadsheets or paper-based systems. They are suitable for small businesses with low inventory levels and simple supply chains.
– Automated
Automated stock control systems use software and hardware to track inventory levels, orders, and shipments. They are suitable for medium to large businesses with complex supply chains and high inventory levels.
– Hybrid
Hybrid stock control systems combine manual and automated processes. They are suitable for businesses that have both low and high inventory levels and can benefit from the flexibility of manual and the accuracy of automated systems.
Components
– Inventory management
Inventory management involves tracking inventory levels, orders, and shipments to ensure that the business has the right products in the right quantities in stock.
– Forecasting and demand planning
Forecasting and demand planning involve using historical data, market trends, and other variables to predict future demand and plan inventory levels accordingly.
– Order management
Order management involves processing orders, allocating inventory, and fulfilling shipments efficiently.
– Receiving and shipping
Receiving and shipping involve managing the inbound and outbound flow of inventory, including inspection, labeling, and tracking.
– Reporting and analytics
Reporting and analytics involve generating reports and analyzing data to identify trends, opportunities, and areas for improvement.
Best Practices for Stock Control Systems
– Regular inventory counts and audits
Businesses should perform regular physical inventory counts and audits to ensure that the system’s data accuracy matches the actual inventory levels.
– Minimizing stockouts and overstocking
Businesses should aim to minimize stockouts and overstocking by using forecasting and demand planning tools.
– Automating key processes
Businesses should automate key processes, such as order management and reporting, to improve operational efficiency.
– Continuously monitoring and adjusting system performance
Businesses should continuously monitor and adjust the system’s performance to ensure that it meets their evolving needs and requirements.
Conclusion
To optimize the benefits of stock control systems, businesses should regularly review and update their inventory management processes, invest in robust stock control system software, and consider the features of a stock control system, such as the Million stock control system, which offers an all-in-one solution for inventory management, forecasting, order management, receiving and shipping, and reporting and analytics. By implementing a stock control system, businesses can improve their inventory accuracy, reduce costs, increase operational efficiency, and enhance customer satisfaction.